Internet of Think: Let the Robots Do It

With robotic process automation (RPA) sparking new ways of doing traditional white collar work and IoT sparking a revolution in data gathering and control, it is time to think again. As one RPA vendor notes on their website blog, “As an automation platform, robotic process automation has the abilities to help manage all the capabilities that Internet of Things now makes possible.”
Automation is no longer something confined to the manufacturing floor. In fact, Pricewaterhouse Coopers (PwC) has estimated that trillions of euros in savings are possible in further automating work tasks, including “whitecollar” activities. This is not about taking away jobs but, rather, empowering individuals to do more and do it better. And, linking these powers to the informationrich IoT world (for example, in the factory or across a retail environment) can further empower decision makers. With IoT extracting data from “everything” and RPA helping to make data actionable, are we perhaps on the cusp of something we could call the “Internet of Think”?
All about RPA
The automation of business processes has acquired tremendous new momentum in recent years, reducing the cost of operations and allowing for the redeployment of capital in more productive directions. Much of this automation has occurred through the continued deployment of fairly familiar technologies, many of which have been honed and improved for more than a generation. However, many tasks have remained resistant to automation. For example, a process such as hiring a new employee can involve providing information to multiple systems at the same time. Since each of the systems are separate, rekeying data is still often required, with all the risks of errors as well as the direct costs that implies. But even these hard tom anlage manual systems are built on rules, even if the rules themselves are well hidden in the habits of employees and not formally documented. Enter robotic process automation (RPA). And don’t be confused by the word robotic, which is something of a misnomer. Rather than parking a hulking automaton at a desk in your accounts payable office, RPA vendors instead aim to have you adopt their software tools, which can automate those manual, rules based tasks. The result of applying these tools is the creation of a virtual robot of sorts – bots in the parlance of the industry – that can thereafter continue to perform a specific process automatically. Often, the bots work hand in hand with existing business process automation systems. The bot creation process varies from vendor to vendor. Many RPA companies now offer forms of artificial intelligence or “machine learning.” Armed with this capability, RPA can quickly grasp the nature of the task and of the data and emulate tasks previously performed by humans. In the example of the employee onboarding mentioned above, an RPA system might be able to quickly record the steps involved and embed the logic in its own activities which would then share the data, as appropriate, between different systems – quickly and minus the clerical errors for which humans are well known.
Today, bots routinely work hand in hand with business.
Machine learning in RPA can speed up the process by making educated guesses about the meaning of specific fields in paper or electronic documents. Bots can also simply “watch” humans perform tasks and come to conclusions about what is going on. For example, a bot watching a human look at accounts receivable documents might notice that values above a certain level in invoices of a certain age caused the human to take a specific action – perhaps flagging the account for a call by a human being. Of course, just like a human assistant, bots may need help or correction from time to time until they reach or exceed human accuracy in performing a task. At that point, the payoff begins because the human can now spend time on more important tasks than simply entering data and making routine decisions. There are, of course, multiple flavors of RPA.
One, often called robotic desktop automation, is a kind of grownup screen scraper, reading a display screen much as a human would and taking steps based on the information it finds. More sophisticated enterprise RPA (ERPA) aims at broader solutions. Based on premises or in the cloud, ERPA tools can detect and create logical paths to model a wider range of processes, harvesting necessary data and making use of other tools and systems, much as a human would. ERPA doesn’t necessarily lock people out of processes but often provides helpful capabilities such as security and even audit trails so, again, ERPA can be kept on a short leash – its actions verified and audited as needed. RPA offerings can also include varying degrees of advanced analytics and machine learning so that they can adapt and change to meet new circumstances; a crucial difference compared to many traditional IT solutions, which often need to be reworked to meet new circumstances by the time they are actually implemented. To be sure RPA is not a magic bullet and can’t solve all business challenges. It is also more complex and requires a bigger commitment of time and talent than, say, a typical packaged software implementation. Interactions between bots also need to be anticipated and understood. Perhaps that is why so many RPA adopters have hailed from the upper ranks of businesses where resources and technical sophistication are greatest. But the benefits can also accrue to smaller organizations (see John Gikopoulos interview) and there is an indication that RPA may soon become a feature of Microsoft Dynamics ERP, which has always focused on the enterprise management needs of midsize companies. While IT may have the skills to help implement RPA, they may not be needed or wanted in the adoption process because RPA functions so closely with activities of the business and relies on the business for its mission definition and training. On the other hand, automation occasioned by RPA may have implications that are broader than simply speeding a few tasks and freeing up human talent, so communicating with IT is probably a good idea. For the faint of heart, of course, integrators and consultants, usually with relationships to an RPA vendor, can help smooth the way Finally, for those worried about entrusting their business to robots, RPA advocates insist people are never really out of the loop and built in safeguards can spot anomalous behavior and show how it occurred. In fact, most of the RPA vendors focus on what might almost be considered a cyborg approach to the subject. Humans will be central but with RPA they will have superpowers. RPA might help bunch, organize, and categorize alerts in a way that makes them more actionable. Sometimes, RPA might be given the power to automate some tasks but a chain of alerts and tools will provide visibility and allow the human to spot problems early and intervene quickly and effectively.
The IoT side
And what about IoT? Ask someone who is deep in the IoT market. “When I went to the Gartner conference last year, there were analysts there who saw RPA and IoT as a natural synergy,” says Abhijit Kakhandiki, vice president of products at Automation Anywhere, an RPA vendor. RPA is about getting work done, not just integrating systems and building connections and a big component is the bot on a machine where the work gets done, he adds. A similar arc is described by Simon van der Jagt, CEO of Nowi. The company was founded in 2015 by van der Jagt and Omar Link. Nowi is a team of 12 people currently with some €2 million invested in product development and with four patents fled. The company is located in Delft, the Netherlands, and is building upon decades of academic research on energy harvesting and power management for low power devices. This knowledge is now being used to solve what they call the power bottleneck in the Internet of Things – namely the fact that IoT is being held back by the need to deliver power to all those sensors and other IoT gadgets.
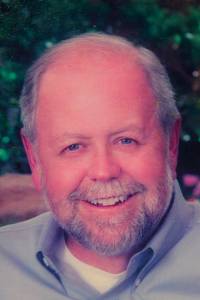
IoT has taken on a number of forms including Industrial Internet of things (IIoT), Internet of medical things (Iomt), and the Internet of everything (IoE)
Pete Smith, TE Connectivity Ltd
“For IoT to succeed we first need to solve the bottleneck of power in wireless sensors,” he adds. Nowi is tackling that challenge by enabling sensor solutions with an “unlimited energy source.” The Nowi Power Module allows sensors to power themselves with what is already available; for example, ambient light, vibrations, or even RF signals such as GSM and WiFi. “There is energy all around us that we can use to power small connected devices,” he explains. And, he hopes, with Nowi technology it will be possible to dramatically multiply the scale and cost effectiveness of the Internet of Things. Then, the data floodgates will open and RPA will need to be ready. “I think that RPA has a lot of different names across industries but it seems to boil down to the same thing. It’s about making things smarter,” says van der Jagt. With RPA, by making things smarter, the process ends up being more efficient, healthy, and productive. “This process of making something smarter differs by application but the underlying principles are always the same,” says van der Jagt – and it’s comparable to human experiences. If a human wants to be smart, he first needs to have senses, needs to be able to smell, touch, hear, taste, etc.
Under pressure: Wireless pressure sensor and transducers such as M5600 and U5600 from TE are used for many industrial and commercial applications.
This is essentially (IoT) data coming in to the system, he notes. Algorithms in the cloud or on premises make sense of the data. “Then we act, say turning traffic lights from red to green, altering a logistics route, or adjusting the temperature output of an air conditioning unit. “In RPA we have this process of sense, think, and act,” van der Jagt explains. Humans can gather data and make decisions but they suffer from interruptions and fatigue. And that’s the problem: without sensors constantly bringing in data, the RPA process quickly comes to a stop. “It is impossible for a smart process to function without having its eyes and ears in the physical world,” says van der Jagt. Some of those eyes and ears are made by TE Connectivity Ltd., a Swiss company that designs and manufactures connectivity and sensor products. “IoT has taken on a number of forms including an Industrial Internet of Things (IIoT), Internet of Medical Things (IoMT), and the Internet of Everything (IoE),” notes Pete Smith, manager of sensor product knowledge and training at the company. Smith explains that the sensors division at TE focuses particularly on harsh environments and is often involved in IoT implementations. Many IoT activities are in factories, “which are often shown as gleaming showcases, with people in lab coats” – the factory of the future. However, Smith notes, many real world customers want to apply factory-of-the-future thinking to existing facilities that look nothing like that. In fact, he notes, many of his company’s sensors are found in steel mills, sewage treatment facilities, and offshore oil plants. Sean Gough, director of product management at the company says the route from IoT sensors to RPA in all those facilities usually starts with local intelligence, where initial analysis can help reduce the deluge of data to something more manageable. “People are working to get to the right level of local analytics so that they are transmitting and analyzing the right level of data at each layer,” he says. Certainly, getting data to where it is needed is a challenge. Hardwiring sensors used to be standard practice, but particularly where customers want to retrofit, “the only practical method is often to use radio,” says Gough. He says the company is now combining sensors and radio in a single device. According to Smith, customers want the ability to integrate as much as possible. In response, the company is making sensors that are digital and adding microprocessors, primarily for self test, so they can know whether the sensors are operating properly, he explains. But the desire to process more at the edge is likely to increase. How much value can you get from automation? “A lot of our customers are on a discovery mission to understand how this will help them,” Smith says. “We think there is no limit,” he adds.
Making the case
Both RPA and IoT have those who claim they can demonstrate strong ROI. Of course, the specifics vary. Some projects produce stellar results and others are not so impressive. However, according to a Tata Consulting Services blog, RPA is demonstrating ROI “in about 25 percent of the time required for a business process workflow solution and 16 percent of the time taken for enterprise application integration to demonstrate significant value.” A recent article posted by ISG Research, “Is IT a Catalyst or Adversary of Your RPA Initiative?,” revealed the results of a survey of 549 European business leaders regarding their adoption of RPA technology and services. One finding was that in EMEA, the CIO is usually responsible or accountable for the RPA buying decision (81 percent)but 57 percent of organizations surveyed said they were stymied in their RPA endeavors by “Lack of IT support” and “Governance/compliance” issues.
The road to RPA: The evolution of robotoc process automation can be seen as a series of steps towards ever increasing levels of automation and artificial intelligence.
The article’s authors, Keri Smith and Aparna Gajanan, observe “if you consider automation a team sport, both the business side and the IT organization must play together to advance the ball.” They also observed that though CIOs often have responsibility for RPA buying, implementation is often handled by others, including CFOs and shared services leaders. Furthermore, despite a widespread belief that RPA is “intuitive” and doesn’t require IT involvement, in fact “RPA is not a plug and play capability; it requires people with technical and business skills to plan, develop, deploy and manage it.” Earlier this year, ISG also weighed in on the broader outlook for advanced business use of RPA in Europe, which they expect will double by 2020, as companies seek to improve customer experience and streamline their finance operations. ISG and Automation Anywhere, an RPA software provider, recently surveyed European business leaders and found that that fewer than 10% of companies will not have begun working on RPA by 2020, while those at an advanced stage will have doubled. While Europe has been slower to adopt technologies like automation than other markets, according to ISG, RPA is actually moving into the mainstream, with 92 percent of respondents saying they anticipate using RPA by 2020, and 54 percent saying they will reach the advanced stage of adoption by then, up from 27 percent currently. Budgets are also up, they said – on average by nine percent in the last year, well ahead of the average increase for general IT spending. Third parties, such as consultants and service providers, make up more than half of this spending.
Over the next 24 months, respondents to ISG say RPA is expected to have the greatest impact on customer service and order processing functions (43 percent), closely followed by finance, treasury, and audit (42 percent), procurement, logistics, and supply chain (40 percent), and sales and marketing (38 percent). The results did not address manufacturing impacts. Among Europe’s largest markets studied by ISG, 60 percent of German companies expect to be in the advanced stage of deployment by 2020 (versus 32 percent today), following by 50 percent in France (up from 22 percent) and 46 percent in the UK (up from 23 percent). However, barriers to adoption remain. Security is a key concern, with 42 percent of businesses citing this as an obstacle to expanding their RPA use. James Dening, vice president Europe at RPA vendor Automation Anywhere, adds: “European enterprises are at an exciting juncture with respect to RPA. If implemented properly, over the next few years RPA technologies will help deliver significant value for businesses across a range of European enterprises and industries, ensuring growth in productivity, efficiency, and output, and helping these firms and industries stay competitive at a local, regional, and global level.”
Impact on employment
According to a recently published article in the USbased Wall Street Journal, Finnish engineering company Wärtsilä Corporation is well along on the RPA path, making plans to deploy more software robots to bring up the efficiency of its finance unit. In part, the investments are in anticipation of the challenges involved with taking on acquired companies in the future. And those financial people currently represent some 750 out of the company’s total headcount of more than 18,000. Improvements in efficiency could have important benefits, according to the article. Since first adopting the “robots” in 2015, more than 100 routine tasks have been reassigned from human workers to robot workers. Certainly, this has all the hallmarks of the all too familiar headlines that predict robots will be eliminating most human jobs. But the story is as familiar as the development of the plow in past millennia or the development of industry more recently: fewer people will be able to produce more. And that has always led to broad economic growth that creates new kinds of jobs – and usually better kinds of jobs. So, expect short term disruption and long term gain. Although there are “horror stories” about people being made redundant through automation, Guy Kirkwood, chief evangelist at UI Path for Europe, based in the UK, says he is not seeing that among customers. Instead, RPA and IoT are actually tending to drive up employee engagement by changing the nature of some work. And, he adds, there is a direct link between employee engagement and customer experience. “So, I expect these technologies to come together over time; I expect the number of people in the back office corporate functions to diminish over time, not through mass redundancy, but through new opportunities,” he says. And, he adds, the number of people doing customer service will rise. “How you deal with customers and how open and approachable and efficient you are will be more important,” he says. And, he notes, “automation” in the form of IoT can have an even more direct link, especially on things like telecom, utilities, or insurance. “IoT is taking off because those companies needed more data; but then the question is what you do with the data and then how you manipulate it,” he adds. Internet of “Think,” as discussed in this article, is about better integration of factory and other corporate functions. All new technologies can have an impact on job opportunities. Most likely, these effects will be gradual and diffuse – and therefore societies will adapt. When change is faster or more disruptive, for example, in a single enterprise or business sector, there may be opportunities for countervailing efforts – training, job creation, or more. However, mostly this is likely to be an opportunity to empower individuals to do more and for society as a whole to benefit with higher productivity. Much like the way ubiquitous word processing technology largely eliminated the typing pools of (mostly) women performing a manual task for others, so too RPA may displace some. But, just as with the casualties among professional typists, many of whom up skilled, using keyboard knowledge as an entry point to other business positions with greater opportunity, so too will those freed from drudge work by RPA find new and often better opportunities.

Shane Nolan, VP Technology, Consumer & Business Services at Industrial Development, Authority (IDA), Ireland
Shane Nolan, SVP Technology, Consumer & Business Services at Industrial Development Authority (IDA) Ireland, says his agency is looking at the potential impact of RPA, IoT, and other emerging technologies on Ireland as both a threat and an opportunity. A first concern, of course, is the potential impact on employment. “We have done some modeling on this and on the one hand you could suggest that AI and RPA will drive jobless economic growth in nations where the capacity for job growth is limited,” says Nolan. In Ireland, particularly, so called shared service centers handling back office or middle office activities are a major source of employment. Companies are usually attracted by lower price points, and the functions are mostly financial, though other functions are becoming standardized and are being provided from a shared service location. At present, some 1,300 multinationals are present in Ireland with 700 of those coming from the US employing about 40,000 people in total. Nolan estimates that about 40 percent of service center activities such as accounts payable and receivables “could be automated tomorrow.” In response, he explains, IDA has developed a strategy and a roadmap for shared services and automation. “We want people to be both concerned and enthused about the potential,” he says. The concern is not just felt in Ireland; it gets to the heart of broader concerns about the future of work. Nolan says the IDA believes it is something where government needs to play a role. “Undoubtedly people will be displaced, so we want to put in place training infrastructure to work with the new technology,” he says. Initial training, for instance, has already been conducted with Blue Prism, an RPA vendor that has ranked high in Gartner’s Magic Quadrant evaluation. Automation Anywhere and UI Path, also RPA vendors, are on the list. “We have developed a full suite of courses with employee federation and the Hackett Group ranging from certificates to college master’s degrees.” Separately, Nolan says IDA is looking for opportunities to embrace other new technologies. “We have a big biopharma industry, especially biotech, that is very next generation and is full of sensors and we also have companies working on autonomous vehicles here,” he explains. Nolan predicts that IoT will create a phenomenal volume of data, beyond what humans can deal with practically, so RPA will be a requirement.
The new wave of technology
Sandwiched between the “executive” level of RPA and the other tendrils of IoT are other technologies that also help complete the picture, including “traditional” robots implemented in hardware. “Looking at the big picture, we are seeing robots becoming more versatile and able to do more than one thing,” says Howie Choset, Professor of Robotics at Carnegie Mellon University School (CMU) of Computer Science in the US. Choset believes one driver will be that high volume, highly customized products will be in great demand in the years ahead and robots can help deliver them. Second, robots are becoming more flexible and easier to install and re purpose, which will be important for low volume, high customization. “We’re also seeing cost reduction in robots and there is a trend toward more collaborative robots (cobots), which are robots working alongside and perhaps directly with people, so they are sharing a common task,” he says.

A key part of digital transformation is having the ability to make data accessible for analysis and to gather insight.
Andy Chang, director of product marketing at KUKA
Among the companies embracing the trend, the largest is Universal Robots, a Danish manufacturer of smaller flexible industrial collaborative robot arms just purchased by Teradyne, a maker of automatic test equipment, he says. “These kinds of robots are smaller and safer to work around and a little bit easier to program, but Universal is not alone,” he says. ABB is another, along with KUKA. Choset says many companies have been slow to embrace robots, cobots, and even RPA. One reason, he notes, is that integration, as with IoT in general, can be challenging. Unlike consumer software or apps for mobile devices, manufacturers “haven’t figured out how to scale; robotic installations are still very customized,” says Choset. “When the industry accomplishes that [better integration], the real discovery of what we can do with automation as well as with data collection will happen,” he says, “and that’s particularly true once robotics is more accessible to SMBlevel companies.”
The KMR iiwa by KUMA, a German market leader, transports material or finished products around the factory.
In part, he notes, it is a matter of having the right standards in place. “It isn’t like you just turn on your robot and off you go; there are many things that haven’t been codified,” Choset says. However, he notes, when the market decides it is needed it will happen. “I think Europeans are making very nice investments in manufacturing robots,” Choset says. “I wish our investments in the US were as big. I think the Europeans are doing a very good job of being progressive, especially public–private partnerships and I think my European colleagues are doing great work,” he adds. Like Choset, Andy Chang, director of product marketing at KUKA, sees room for more robust standards and protocols. “A key part of digital transformation is having the ability to make data accessible for analysis and to gather insight. Today’s new technologies must be developed using standard protocols and open interfaces to allow existing robotic technologies to be part of new IoT or Industry 4.0 practices,” Chang says. For its part, KUKA has been heavily investing in cloud, web, and mobile technologies to augment existing mechatronic systems. “A product we currently offer is KUKA Connect – a software platform that leverages cloud computing technologies and big data – to provide users access and analytics of their KUKA robots at any time and on any device,” Chang says. KUKA Connect, and other similar cloud based technologies, will allow manufacturers to implement robot centric IoT and Industry 4.0 solutions to their operations, enabling them to create their factory of the future. In addition, “we’re also looking at how we can integrate existing IT technologies from backend ERP systems with relevant technologies, such as Salesforce, to better combine business needs and customer demands,” says Chang. These developments, he believes, will fundamentally change individual companies, as well as transform market dynamics across a whole range of industries in countries all around the world – in both the developed as well as the emerging markets. “At the end of this transformation process, successful industrial companies will become true digital enterprises, with physical products at the core, augmented by digital interfaces and databased, innovative services,” he says. Insights gained through the convergence of IT and operational tech (OT) will fuel better internal business decisions, higher quality products, and faster delivery times, he believes. KUKA is also thinking about the role of AI. But, while there is promise in all those new technologies, including AI, at least one executive warns against taking buzzwords at face value. That is the case with JeanPhilippe Baert, COO of Arago, a German AI company based in Frankfurt am Main. He notes that his company was established in 1995 by CEO Chris Boos to focus on artificial intelligence. Today, it applies that technology to process automation and, in particular, through HIRO™ its general problem solving artificial intelligence technology. Baert says the company has been able to achieve over 87 percent automation of processes with its customers, which now number more than 30 globally. “Anything could be run by AI to help companies be more flexible and grow faster,” he says. Baert explains that his company is based on AI that goes beyond most other AI; it can learn and solve new issues that were unknown until now And while there isn’t a direct link to IoT, Baert says IoT provides the ability to collect and analyze more data. “The combination of applying AI to the data analytics and the environment of the IoT edge may make possible new capabilities,” he says. For example, in the case of optimizing electricity consumption of a building or a city, you can have a perfect algorithm, but it will probably never be as well optimized as what HIRO can do by using data to be precise, rapid, and accurate, he explains.
Baert says that understanding, learning, and solving is what is handled by HIRO. This process is abetted by a semantically organized map that makes the logic relevant to, say, a city, an oil company, a hospital, or a travel agency. When it comes time to solve a problem, the HIRO engine goes into action. “This can be important in IoT because IoT will monitor all the flows and all the information; HIRO through its reasoning approach will be able to learn through those changes and arrive at solutions that could not have been done before. “Tomorrow you will have super tankers or ferries that can operate without a crew; not just as a matter of navigating with GPS but for anything that occurred or could occur, the intelligence will be able to solve the problem or prevent the problem,” says Baert.
Internet of Think: RPA takes to the air
Arago is helping Lufthansa Technik, the maintenance division of the German airline, to provide dramatic process optimization on the flow of activities and tasks that are performed by the employees. Aircraft regularly undergo light, medium, or high maintenance programs. All those maintenance operations can take a lot of time for the repetition of many, many manual tasks and each must be performed precisely, in accordance with regulations. “What we’ve done is not to change the task, because they are mandatory and compulsory, but instead we have optimized the flow of the process and the environment and the access to resources and have provided a better sequence of engagement depending on the environment,” says Baert. The impact for the airline company has been huge. It is a theoretical number, but we can decrease from ten to fve days per year that the plane has to be on the ground for maintenance. “It is only through reasoning by AI that we can do that,” he adds. Needless to say, those business impacts become fodder for RPA and high level management consideration. Another view on the IoT–RPA link comes from Automation Anywhere’s Kakhandiki. “We find with RPA there is a very current trend; there has been an explosion of data through digitization and analysis and for the first time, data is accessible and visible,” he says. “It is coming not just from digitization of processes but from IoT and sensor data,” he adds.

Abhijit Kakhandiki,Vice president of products at Automation Anywhere
“In our view, as IoT becomes bigger and bigger there is a natural play between IoT and RPA,” Kakhandiki says. When you create a bot on his company’s platform you can log any data or any business event. The data can be from a system or sensor in IoT. And, as data streams expand, “bots can deal with exponential volume increases,” he says. And it’s not just theoretical. Kakhandiki says his company has set up a bot store to help people enhance their RPA ecosystem. For example, he says, “we have bots in our store that can interface with GE Predix, General Electric’s software platform for the collection and analysis of data from industrial machines.” Another pretreated bot can work with the C3 IoT, a platform as a service (PaaS) for the rapid design, development, and deployment of the largescale big data and predictive analytics. “You can take that data and now suddenly it is available to your RPA where you can further make use of it,” says Kakhandiki.
Making the dream come true
“RPA and cognitive automation are rapidly being deployed throughout the world, across industries,” says Dening at Automation Anywhere, one of the largest RPA vendors. The lure, he notes, is that AI trained algorithms that are part of RPA initiatives work 24 hours a day without complaint, require little oversight, and can quickly and easily scale. “Because the barriers to implementation are so minimal, there’s little reason for most enterprises to delay piloting RPA on a limited basis,” Dening notes. In most cases, company leaders will see tangible and measurable results within a few weeks rather than months, he explains. Today, most large companies are now engaging with RPA to some extent – the business drivers are primarily about reducing cost and increasing operational efciency, “with the expectation to move or be seen to be moving to a more digitally oriented business,” Dening says. While Dening says he has not yet encountered any examples of companies integrating RPA and IoT or making plans to build it into their automation and digitalization strategy, that doesn’t mean it’s not going to happen. “They’re not inherent bedfellows, and there is much lower hanging fruit for RPA in finance, HR, operations and the like,” he says. However, as enterprises get connected, Dening says he expects more RPA/IoT use cases to crop up in the next couple of years. However, the caveat is that “given that we know IoT is going to be a ‘lots oft hings’ technology, the tools to manage large estates will be built into IoT platforms from day one, needing less retrofitting of tech that deals with scale, which is often what RPA is used for,” Dening adds.
“What is really driving the growth of RPA is the adoption rate of automation across organizations around the world and across all industries,” says Guy Kirkwood, chief evangelist at UI Path, based in the UK, which claims 45 percent of its revenue from North America, 34 percent from Europe, and 24 percent from Asia Pacifc, with 18 locations across 14 countries. “All the vendors in RPA are growing fast, but we’re the fastest; we have a thousand people in the business and revenues just topped $100 million, up from just $1 million 24 months ago,” he says.
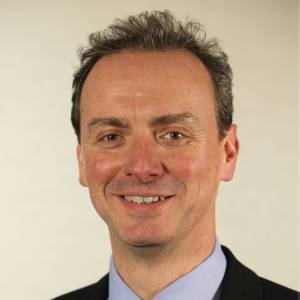
RPA and IoT are tending to drive up employee engagement by changing the nature of some work.
Guy Kirkwood, chief evangelist at UI Path for Europe, UK
That, he claims, is one of the fastest ever recorded in the software industry, which allows them “to play in Google’s playbook.” Underscoring his comments are the venture investments his company has received, including from the venture arm of Alphabet (Google). Kirkwood says, jokingly, that the old mantra used to be that no one ever got fired for buying IBM, but in his view that thinking is no longer holding up with the new waves of innovation. “We’re seeing the rise of an RPA ecosystem driving adoption and the convergence of multiple technologies,” he says. He also credits his own company for seeding that ecosystem. “All the RPA vendors charge for training, including us when we joined the industry, but now we give it away,” he says.
UI Path launched its free academy last year and since then over 200,000 people have gone through the RPA training program. That’s an especially significant number because it includes not only developers and techies but many non traditional business roles as well, yielding a broad field of UI Path developers active in 70 countries.
High potential: Areas and industries where RPA can make the biggest difference according to analyst from Everest Group.
Digital transformation
For Kirkwood, the rise of RPA and IoT is essentially about the broader growth of digital and its trans formative power. “Every organization is undergoing transformation; RPA is a really good first step on the journey because it is relatively quick and relatively cheap and the ROI is really good,” he says. For example, working with the UK’s Department for Work and Pensions (DWP), which is responsible for welfare, pensions, and child maintenance policies and ranks as the country’s biggest public service department, UI Path was able to go from concept to process in 12 weeks. “They expected it to be six to nine months and now on the pilot alone they are saving 6 million pounds annually,” Kirkwood says. For UI Path and others, the “ecosystem” is helping to spread RPA. “Consultants use RPA to demonstrate digital transformation and they use that as the starting point because returns are so quick,” he says. Large independent software vendors such as Microsoft and Oracle are also anxious to put RPA into their platforms because of its inherent value but also because it opens doors to new buyers. “We are dealing with operators at different levels and also cutting across so many industries so they see it as a route to new markets,” Kirkwood explains. Last year UI Path did a deal with Oracle whereby UI Path is built into their cloud business. For anyone buying Oracle cloud, the software robots are already there, waiting to be switched on. And, Kirkwood notes, his company is discussing building UI Path into Microsoft Dynamics – the midmarket ERP offering.
Looking ahead
What does the future hold for more fully integrating information flows across businesses – from IoT and robots to business functions such as planning, billing, inventory management, and marketing? Where is RPA starting to have an impact? The answers are not yet clear. However, notes Chang, both automation and overall business processes will need to improve and transform to accommodate the increased demand from consumers. In today’s market, “the customer is the most disruptive force and the most influential driver behind product design, development, and delivery,” he says. To remain competitive in their respective markets, manufacturers will be required to implement an integrated system that includes a customer facing platform, he says. “At the end of the day, RPA is about processes – analyzing them, understanding them, and then automating them,” says Harel Tayeb, CEO of RPA vendor Kryon. He says RPA’s interaction with IoT is fascinating because, as the everyday objects with which we interact become “smart,” the types of processes and the quantity grow exponentially. “Think of what you can do with the programs on only a desktop computer compared to a world in which our houses can be programmed, our cars, our lives,” he says. “It opens up an entirely new range of opportunities for RPA, which is exciting on a consumer level as well as a developer level,” Tayeb adds.

Sign up for the Avnet Silica Newsletter!
Stay up-to-date with latest news on products, training opportunities and more!

Take a DEEP look into the future!
Get the latest market trends and in-depth trainings on our Digital Event Experience Portal!

Avnet Silica Design Hub
Browse and review hundreds of proven reference designs to accelerate your design process. Our designs can be modified and saved in our AVAIL design tool and then exported to your CAD tool of choice.



